The integration of press brake technology with sheet metal stamping processes presents a revolutionary approach to metal fabrication, enabling enhanced efficiency, precision, and productivity. This comprehensive article explores the synergies between press brake and sheet metal stamping technologies, highlighting the benefits, challenges, implementation strategies, and future prospects of integrating these cutting-edge techniques.
By combining the precision of press brake bending with the versatility of sheet metal stamping, manufacturers can achieve superior results in forming and cutting operations, ultimately leading to accelerated production speeds and improved product quality.
Metal fabrication encompasses a wide range of processes, from bending and forming to cutting and stamping, each serving a crucial role in the manufacturing industry. The integration of press brake technology with sheet metal stamping represents a symbiotic relationship that leverages the strengths of both techniques to streamline production processes and elevate the standards of metal component manufacturing. This article delves deep into the fusion of press brake technology with sheet metal stamping, elucidating the transformative impact it has on efficiency, precision, and productivity in the metal fabrication sector.
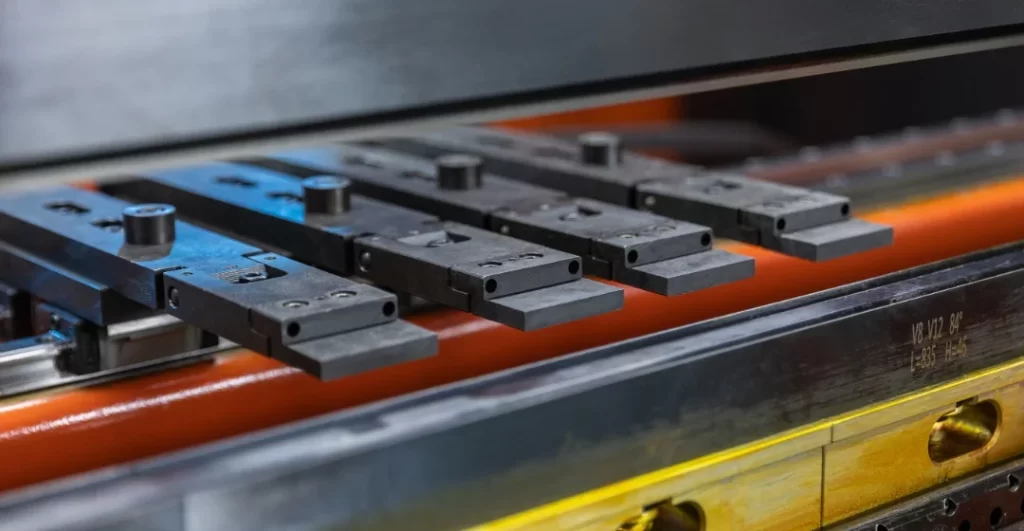
Benefits of Integration:
1. Enhanced Precision and Accuracy:
By combining the controlled bending capabilities of press brake technology with the intricate stamping processes of sheet metal stamping, manufacturers can achieve unparalleled precision and accuracy in forming complex geometries and profiles on metal sheets.
2. Increased Efficiency and Productivity:
The integration of press brake and sheet metal stamping technologies leads to a seamless workflow that optimizes production efficiency, reduces downtime, and boosts productivity levels, resulting in faster lead times and higher output volumes.
3. Improved Product Quality:
The precise control and repeatability offered by integrated systems ensure consistent quality and uniformity in formed and stamped metal parts, minimizing defects, rework, and material wastage.
4. Versatility in Applications
The integrated approach caters to a diverse array of industries and applications, ranging from automotive and aerospace to construction and electronics, providing manufacturers with a versatile and flexible solution for their metal fabrication requirements.
5. Cost-Effective Solutions
Through optimized production processes, reduced scrap rates, and enhanced operational efficiency, the integration of press brake technology with sheet metal stamping delivers cost-effective solutions that yield long-term savings and improved profitability for manufacturers.
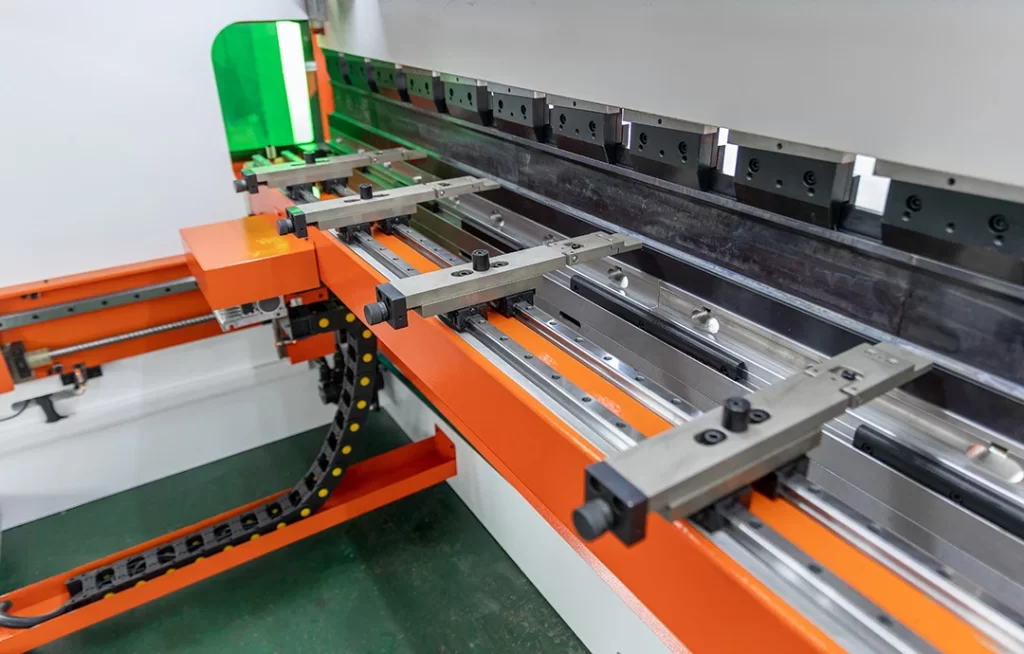
Challenges and Solutions:
1. Equipment Compatibility
Integrating press brake technology with existing sheet metal stamping equipment may present challenges in terms of compatibility and synchronization. To overcome this, manufacturers can invest in retrofitting or upgrading equipment to ensure seamless integration and interoperability.
2. Operator Training and Skills Development
The successful implementation of integrated systems requires skilled operators and technicians who are proficient in leveraging the capabilities of both press brake and sheet metal stamping technologies. Training programs and knowledge-sharing initiatives can bridge the skills gap and enhance workforce competencies.
3. Maintenance and Calibration
Regular maintenance, calibration, and upkeep of integrated systems are essential to sustain optimal performance, accuracy, and reliability. Establishing robust maintenance protocols and scheduling preventive maintenance activities are critical for prolonging equipment lifespan and minimizing downtime.
4. Financial Considerations
While the initial investment in integrating press brake technology with sheet metal stamping processes may require a significant financial outlay, the long-term benefits in terms of increased efficiency, productivity, and quality justify the expenditure. Manufacturers should conduct a thorough cost-benefit analysis to assess the return on investment and evaluate the feasibility of integration.
Implementation Strategies:
1. Equipment Assessment and Upgrade
Evaluate the compatibility of existing press brake and sheet metal stamping equipment for integration, and invest in upgrades or retrofits if necessary to ensure seamless alignment and functionality.
2. Operator Training and Skill Development
Provide comprehensive training programs and hands-on workshops for operators and technicians to familiarize them with the integrated systems, operational procedures, safety protocols, and troubleshooting techniques.
3. Maintenance Protocol Establishment
Develop standardized maintenance protocols, schedules, and checklists for integrated systems to facilitate regular inspections, calibration, lubrication, and preventive maintenance activities, ensuring optimal equipment performance and longevity.
4. Performance Monitoring and Evaluation
Implement a robust system for monitoring key performance indicators, such as production speed, output quality, scrap rates, downtime, and cost savings, to track the effectiveness of the integration and identify areas for improvement and optimization.
The integration of press brake technology with sheet metal stamping processes marks a paradigm shift in the metal fabrication industry, revolutionizing the way manufacturers shape, form, and cut metal components. By harnessing the synergies between these advanced technologies, manufacturers can unlock new levels of efficiency, precision, and productivity, positioning themselves for success in a competitive marketplace.
Through strategic planning, investment in training and skills development, regular maintenance, and performance monitoring, manufacturers can harness the full potential of integrated systems to achieve greater operational excellence, cost savings, and customer satisfaction. As the demand for high-quality, customized metal components continues to rise, the integration of press brake technology with sheet metal stamping provides a winning formula for manufacturers seeking to stay ahead of the curve and drive innovation in metal fabrication processes.