In the realm of manufacturing and fabrication, precision is key. One of the essential tools that ensure accuracy and efficiency in shaping pipes is the automatic pipe bending machine. This article delves into what these machines are, their components, working principles, applications, and benefits.
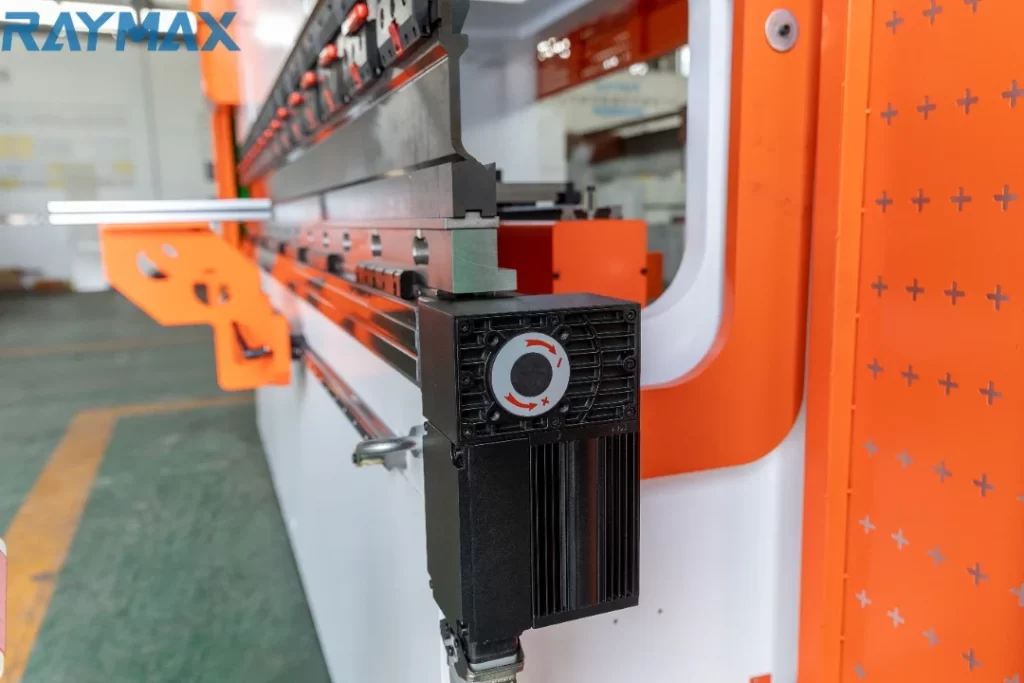
What is an Automatic Pipe Bending Machine?
An automatic pipe bending machine is a specialized piece of equipment designed to bend pipes and tubes into various shapes with high precision and minimal manual intervention. Unlike manual bending processes, which can be labor-intensive and prone to human error, automatic machines streamline the operation, allowing for faster production rates and consistent quality.
Key Components
Control System: Most automatic pipe bending machines come equipped with advanced control systems that allow operators to program specific bending angles and parameters. These systems can be computer-based, utilizing CNC (Computer Numerical Control) technology.
Bending Arm: The bending arm is the core component responsible for executing the bends. It moves in a controlled manner to apply force to the pipe at predetermined angles.
Pipe Holder/Clamp: This component holds the pipe securely in place during the bending process, preventing slippage and ensuring accuracy.
Hydraulic or Electric Motor: Depending on the design of the machine, it may use hydraulic or electric power to drive the bending process, offering different advantages in terms of speed and force.
Safety Features: Automatic machines are often equipped with sensors and emergency stop mechanisms to ensure operator safety during operation.
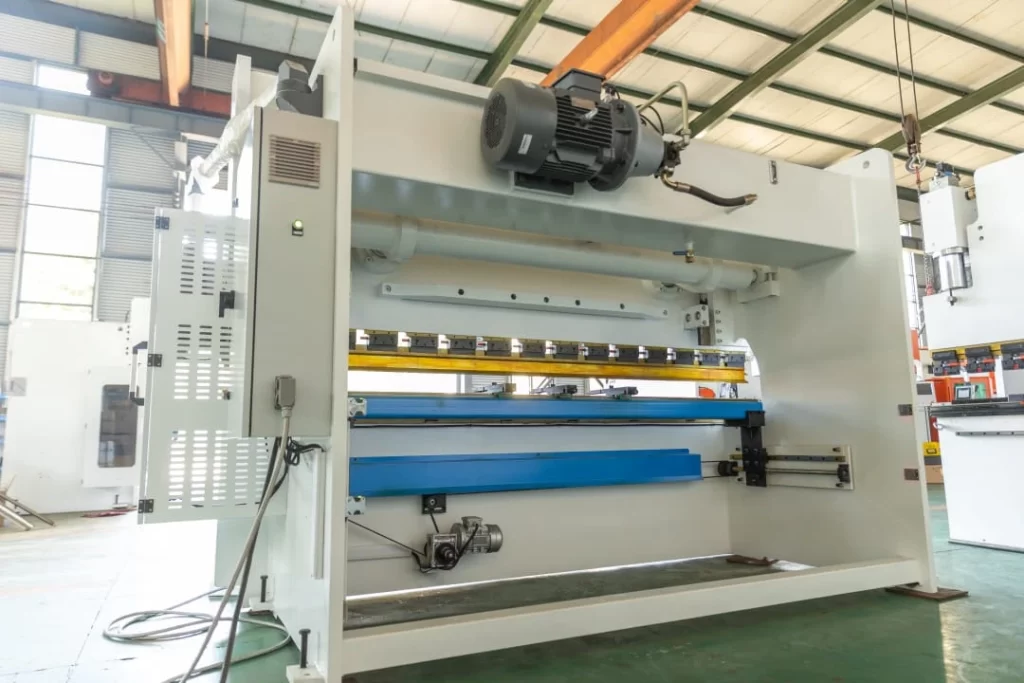
How Does It Work?
The operation of an automatic pipe bending machine generally involves several steps:
Input Parameters: The desired specifications (angle, radius, and type of bend) are programmed into the machine's control system.
Loading the Pipe: The pipe is securely clamped into position by the machine.
Execution of Bend: The control system activates the bending arm, which moves in a precise path to create the specified angle without damaging the integrity of the material.
Quality Check: After bending, some machines have integrated quality inspection systems to verify dimensions and angles, ensuring they meet the required specifications.
Applications
Automatic pipe bending machines find extensive applications across various industries, including:
Automotive: Used for creating exhaust systems, roll cages, and other structural components.
Construction: Employed in fabricating handrails, staircases, and structural supports.
HVAC: Essential for making ducting and piping systems.
Shipbuilding: Used in the production of pipes for fuel, water, and hydraulic systems.
Furniture Manufacturing: Utilized for creating unique designs in metal furniture pieces.
Benefits of Using Automatic Pipe Bending Machines
Increased Efficiency: Automation significantly reduces the time taken to produce bent pipes, allowing for higher output rates.
Consistency and Precision: With programmed settings, the machine delivers uniform results with minimal variations, enhancing product quality.
Reduction in Labor Costs: Fewer manual interventions mean lower labor costs and reduced risk of human error.
Versatility: Many modern machines can handle a wide range of pipe sizes and materials, making them adaptable to various projects.
Enhanced Safety: Automatic machines reduce the physical demands on workers and incorporate safety features to mitigate risks associated with manual bending processes.
Conclusion
The advent of automatic pipe bending machines has revolutionized the way industries approach pipe fabrication. By combining advanced technology with mechanical engineering, these machines provide solutions that are efficient, precise, and adaptable to numerous applications. As industries continue to evolve, the role of automatic pipe bending machines will only grow in significance, making them indispensable tools in modern manufacturing.