In the realm of metal fabrication, precision, efficiency, and accuracy are paramount. To meet the evolving demands of modern manufacturing processes, the integration of Computer Numerical Control (CNC) solutions for press brakes and shears has emerged as a game-changer. This article delves into the transformative impact of CNC technology on press brakes and shears, highlighting how these advanced systems revolutionize metalworking processes, streamline operations, and elevate productivity to new heights.
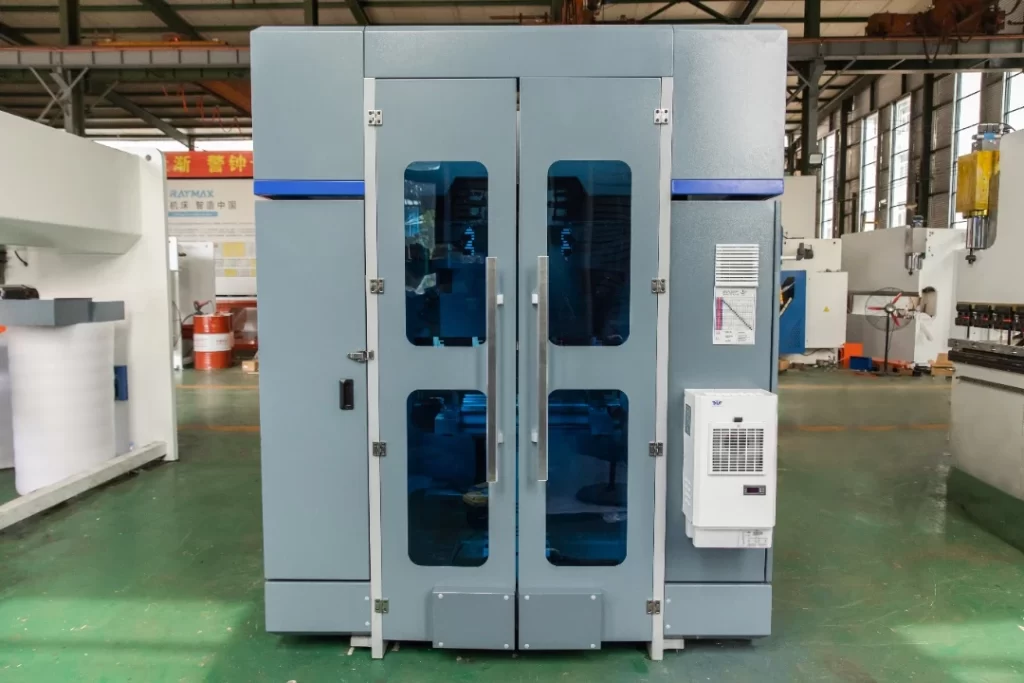
Enhanced Precision and Accuracy:
CNC solutions bring a new level of precision and accuracy to the operation of press brakes and shears. By eliminating manual adjustments and human errors, CNC-controlled machines ensure consistent bending angles, cutting dimensions, and material positioning with remarkable accuracy. The ability to program specific parameters and geometries into the CNC system enables operators to achieve intricate designs and complex shapes with unparalleled precision, thereby enhancing the overall quality of fabricated parts.
Increased Efficiency and Productivity:
One of the key benefits of incorporating CNC solutions in press brakes and shears is the significant boost in operational efficiency and productivity. Automated processes, rapid tool changes, and optimized cutting sequences facilitated by CNC technology minimize downtime, increase throughput, and expedite production cycles. With the ability to run continuous operations, monitor progress in real-time, and execute complex tasks swiftly, CNC-controlled machines empower metal fabricators to meet tight deadlines, handle high-volume orders, and maximize output with efficiency.
Versatility and Flexibility:
CNC solutions offer unparalleled versatility and flexibility in adapting to diverse fabrication requirements. The programmability of CNC systems allows for quick setup changes, tool reconfiguration, and seamless transitions between different bending angles or cutting profiles. This flexibility enables manufacturers to accommodate a wide range of materials, thicknesses, and geometries without the need for extensive manual adjustments, offering agility and adaptability to meet varying customer demands and project specifications.
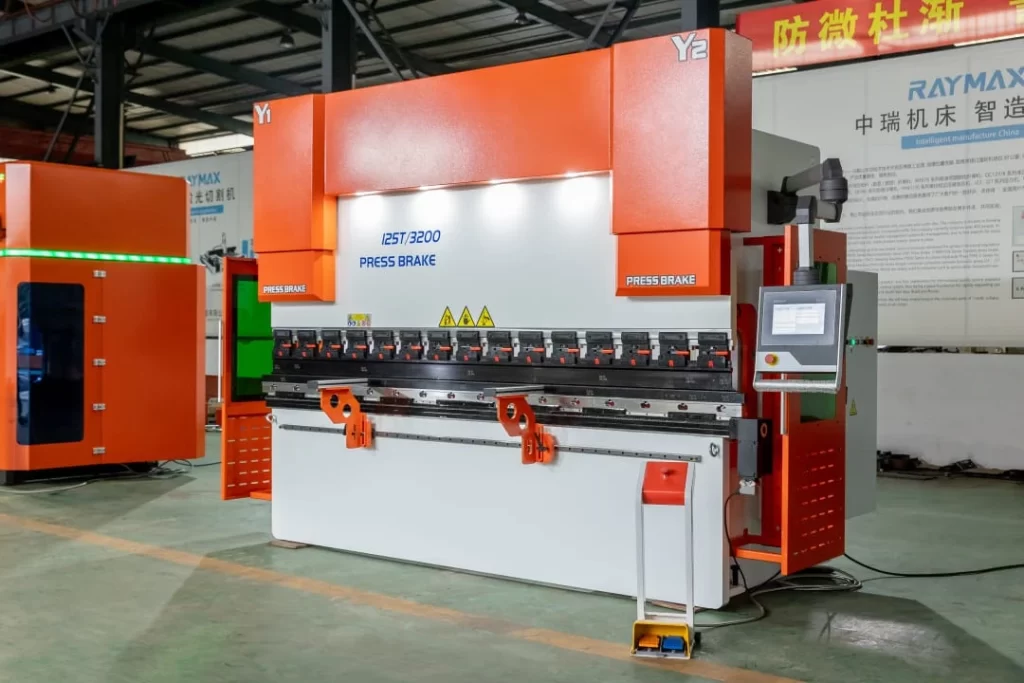
Advanced Features and Customization:
Modern CNC systems for press brakes and shears come equipped with a plethora of advanced features and customization options that cater to specific fabrication needs. From intelligent tooling recognition and adaptive bending algorithms to real-time monitoring and predictive maintenance capabilities, CNC technology enables metal fabricators to optimize machine performance, reduce material waste, and enhance operational control. Customizable software interfaces and programming functionalities empower operators to fine-tune settings, create tailored workflows, and maximize the functionality of CNC-controlled machines according to their workflow preferences.
Future Trends and Innovation:
The integration of CNC solutions for press brakes and shears continues to evolve with ongoing technological advancements and industry innovations. The incorporation of Artificial Intelligence (AI), Internet of Things (IoT), and data analytics into CNC systems is driving the next wave of transformative capabilities, enabling predictive maintenance, remote monitoring, and adaptive control features to further enhance operational efficiency and performance. As the metal fabrication industry embraces digitalization and smart manufacturing concepts, CNC solutions are poised to play a central role in shaping the future of metalworking processes and revolutionizing the way components and structures are fabricated.
The adoption of CNC solutions for press brakes and shears represents a paradigm shift in the metal fabrication landscape, empowering manufacturers with unprecedented precision, efficiency, and flexibility in their operations. By leveraging the capabilities of CNC technology, metal fabricators can elevate their production processes, optimize resource utilization, and deliver exceptional quality components with speed and accuracy. As CNC technology continues to advance and integrate with emerging trends, the future of metal fabrication holds limitless possibilities for innovation and progress, setting new standards for excellence in the manufacturing industry.
As a leading manufacturer of sheet metal fabrication machinery, our focus on the development of press brakes remains paramount. We are dedicated to pioneering CNC solutions that redefine precision and efficiency in sheet metal processing. By visiting our website, you can delve deeper into the realm of sheet metal fabrication machinery, gaining insights into the latest technological advancements and innovative solutions. Join us in shaping the future of sheet metal fabrication through our commitment to excellence and cutting-edge press brake technology.