Press brake operations are at the heart of metal fabrication, where precision and efficiency are paramount. The golden rules of press brake operation serve as a foundation for producing high-quality formed parts while maintaining safety and operational integrity. In this blog, we will explore the essential guidelines that every operator should follow to optimize their press brake operations.
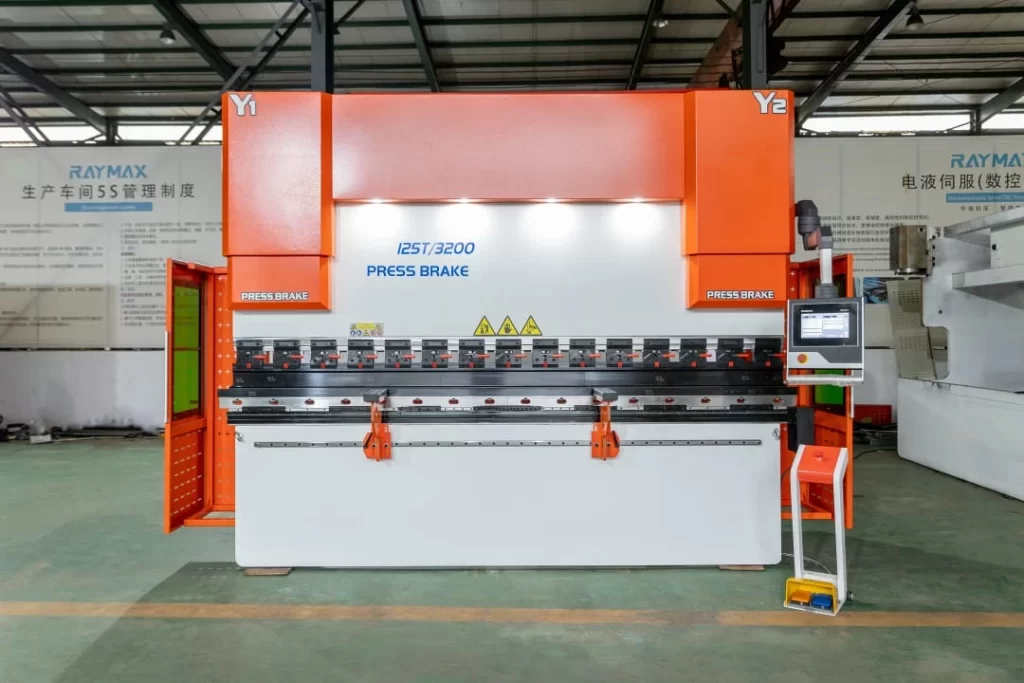
The Importance of Tooling:
The first golden rule emphasizes the critical role of tooling in press brake operations. High-precision tools, manufactured within tight tolerances, are essential for achieving part accuracy without the need for shimming or other adjustments during setup. The quality of the tools directly impacts the quality of the final product.
Tool Selection and the Rule of 8:
Selecting the appropriate tools for the job is the second golden rule. The "Rule of 8" suggests that the V-die opening should be eight times the material thickness for optimal bending. However, this rule may need to be adjusted based on the specific requirements of the part, such as the desired bend radius or flange length.
Safety Protocols:
Safety is non-negotiable in any manufacturing environment. Press brake operations must adhere to strict safety protocols, including the use of personal protective equipment (PPE), ensuring that safety guards are in place, and never removing a part from the press brake while the ram is down.
Operator Training:
Effective training is the third golden rule. Operators must be well-versed in the capabilities of their press brake, including how to program the control system and how to recognize potential issues that could arise during operation.
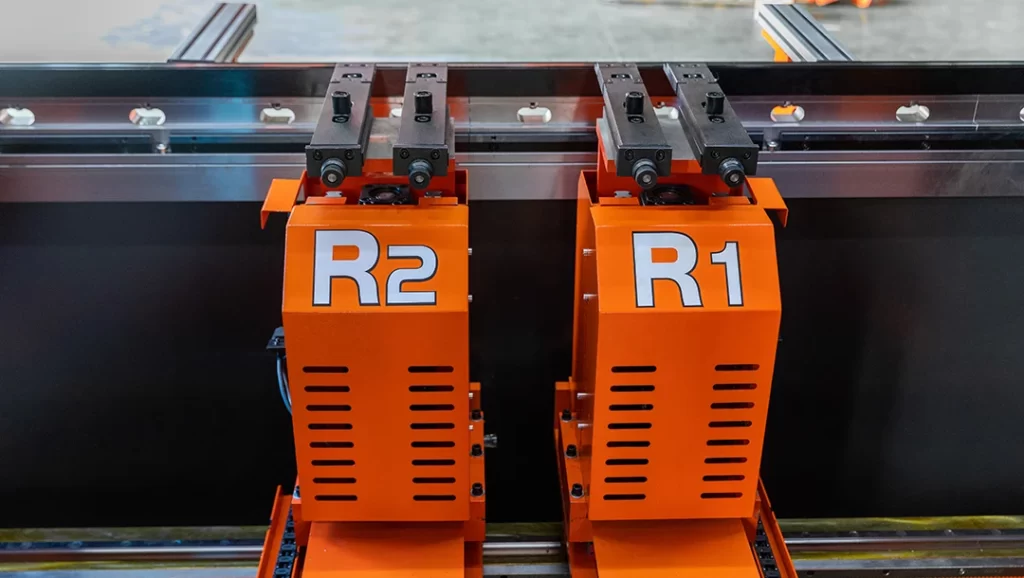
Setup Efficiency:
Minimizing setup times is crucial for maintaining efficiency. This involves having a systematic approach to tool changes and die selection. Having duplicate sets of tools for each press brake can significantly reduce the time spent searching for the correct tools.
Quality Control and Maintenance:
Regular inspection and maintenance of tools and machines are the fourth and fifth golden rules. Worn or dirty tools can compromise the quality of the formed parts and pose safety risks. Similarly, well-maintained machines operate more efficiently and safely.
Material and Bending Precision:
Understanding the material being formed is essential. Different materials may require different tooling or adjustments to the press brake settings. Using segmented sections for tooling allows for precise bending without shimming, ensuring consistent part quality.
Efficient Workflow:
Organizing the press brake area efficiently can streamline the workflow. This includes having tools and materials readily accessible and minimizing unnecessary movement around the machine.
By following these golden rules, press brake operators can ensure that they are working in a safe, efficient, and productive manner. Adhering to these guidelines not only enhances the quality of the formed parts but also contributes to a safer and more effective work environment. As the metal fabrication industry continues to evolve, these golden rules will remain the cornerstone of successful press brake operations.
In wrapping up our discussion on the golden rules of press brake operation, we have highlighted key principles essential for safe and efficient bending processes. As a reputable manufacturer of press brake machines, with our machines being among our best-selling products, we prioritize delivering high-quality equipment and export services to meet the diverse needs of our customers worldwide.
To explore our range of top-of-the-line press brake machines and discover how our solutions can enhance your metalworking operations, we encourage you to visit our website. Experience firsthand the precision, reliability, and innovation that define our products and make us a trusted leader in the industry. Click now to access more information and unleash the potential of our press brake solutions.